Experience the Unmatched Precision of Remington Rimfire Ammunition
- By Admin
- August 3, 2023
- 03:08 PM
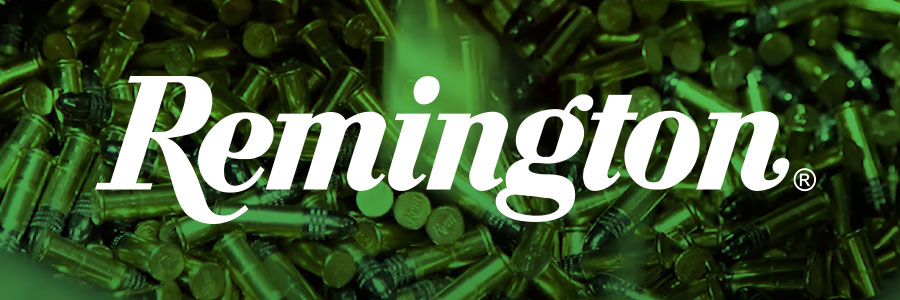
Welcome to the heart of Remington Ammunition's rimfire manufacturing plant in Lonoke, Arkansas, where innovation meets tradition to create the finest .22 rounds in the USA. Step into a world of cutting-edge technology, time-tested expertise, and a legacy of excellence that shooters worldwide trust and love.
Rimfire vs. Centrefire: The Sizzling Showdown
Rimfire's charm lies in its lightweight, compact design and budget-friendly appeal. While centrefire ammunition may hog the limelight, rimfire's affordability makes it a favourite for small game hunting, sports shooting, and casual target practice.
Remington Rimfire: Where Legend Meets Perfection
Step into the realm of Remington rimfire, where craftsmanship meets automation on an unparalleled scale. Our state-of-the-art machinery, custom-made by DuPont, churns out bullets at breakneck speeds without compromising precision. From the .22 Viper to the .22 High Speed, our wide range ensures shooters find their perfect match.
Shooters globally know and trust Remington rimfire, from .22 LR to .22 WMR and the .17 HMR.
“We have six or seven different operations dedicated to making .22 rounds,” explained Rimfire Loading Technician Anthony Terry. “There’s the .22 Viper, .22 Yellowjacket, SubSonic and .22 Short - the .22 TV, .22 Hollowpoint and .22 High Speed are hot sellers.”
The Lonoke facility has some of the world’s fastest rimfire manufacturing machinery, custom made by DuPont employees at the plant’s inception. Remington’s rapid, proprietary rimfire processes are continually optimised and meticulously maintained.
The Art of Ammunition Manufacturing
Witness the intricate process that transforms brass strips into the iconic rimfire shells. Remington's proprietary automation delivers volumes of bullets faster than any other process, all while maintaining the highest standards of quality and consistency.
Testament to Remington’s unmatched quality and consistency, their machines work as efficiently now as they did when they were created in 1950.
Like centrefire rounds and shot shell caps, Remington rimfire cases are stamped out of brass strips - though these smaller, low pressure rounds undergo a shorter overall process. Once shell cups are stamped, they’re completed with a head stamp and rim. Annealing and washing follows, then primer is added.
Secrets of the Primer
Each shell receives the perfect amount of primer, ensuring flawless performance and reliability. No misfires, no compromises. Remington primer is made in 20 lb batches containing seven different chemicals. The primer mix starts out quite wet, with around 20% moisture, and is made in 1 lb ‘cups’ from which primer pellets are derived.
The primer cups are placed onto a charge plate (template) featuring indentations with a specific thickness and hole diameter to create precisely weighted primer pellets - key to ensuring each shell receives the right amount of primer.
The charge plates are fed into a spinning pin punch mechanism that spills primer mixture from the pellets into the rims of shells passing underneath. It’s crucial that the entire rim of the shell is covered with primer to prevent shell voids that cause misfires. Following this, the shells are dried for several days.
Precision in Every Shot: Rigorous Testing
Quality is non-negotiable at Remington. Rounds undergo rigorous testing, ensuring each one meets our impeccable standards. With a keen eye and cutting-edge technology, our craftsmen analyse every round for precision and performance, leaving no room for imperfections.
Remington’s rimfire testing process is similar to other ammo types, but uses far higher quantities. Shells are analysed by a special camera that checks the base of each round to ensure correct primer application. Imperfect rounds are easily spotted and removed from the production line.
To test the rounds practically, Remington’s craftsmen use barrelled actions on a Remington 40x single shot platform that fire and eject cartridges automatically.
The ammunition testers need only to reload the guns, a fast, safe and efficient method that allows them to focus on assessing shell performance and quality via the transducer and velocity screens, which rapidly gather detailed velocity, pressure and accuracy statistics.
For every sample fired, data is fed back to the loading area to make minute adjustments, improving Remington’s manufacturing process in real time.
Ready for Action: Packing and Shipping
Once our rounds pass the ultimate tests, they are meticulously packed and shipped to customers. From the factory to your hands, Remington takes pride in delivering ammunition that exceeds expectations and brings joy to shooters everywhere.
“Once everything’s tested we get the ammunition packed and shipped, and we have some happy faces when our customers receive their rounds,” laughed Terry.
“Rimfire is in high demand right now,” stated Vista/Remington President Jason Vanderbrink. “CCI is the world leader in rimfire, Federal is a great brand too. We want to bring our expertise to help Remington rimfire - without changing it."
“Short-term, we’re going to heavily load our rimfire business, becoming more efficient over time. Our main goal is to give consumers more options, which we aim to do with the Remington rimfire brand.”
Embrace the Remington Rimfire Experience
Join the ranks of skilled marksmen who swear by Remington rimfire. We're here to cater to your shooting needs, offering unparalleled variety and performance without compromise.