Setting out to see what makes optics tick
- By FRANK MELLONI
- April 1, 2024
- 12:04 PM
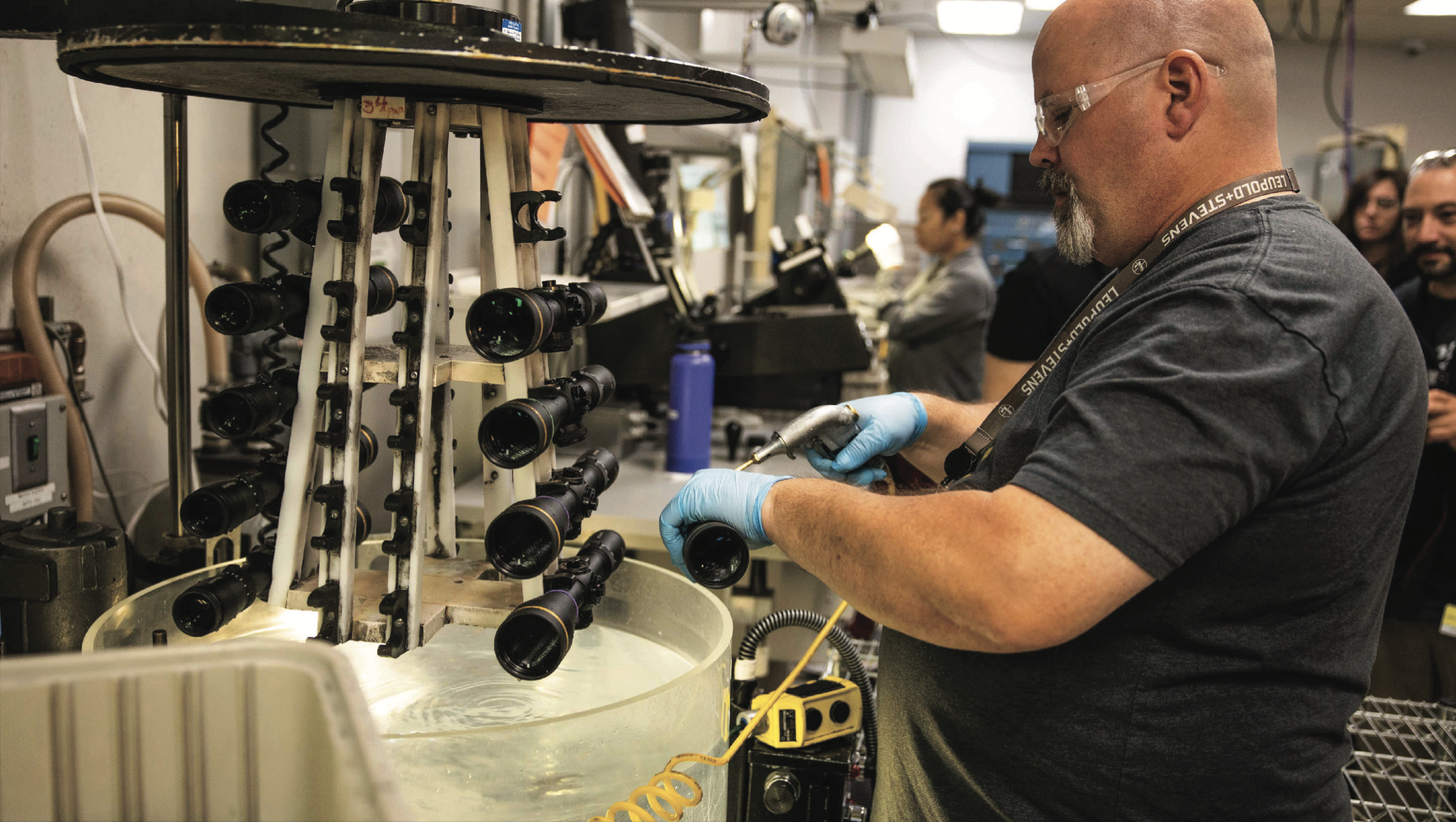
We spin the turrets, place the reticle on target, adjust the parallax, fire a round, and observe our point of impact.
If the shot lands where intended, we move on. For many of us, little thought goes into the process that made the preceding sequence of events line up with the intended outcome. It’s a scope; they just work, right? Not quite. Admittedly, I used to fall into this camp, believing that quality optics can be mass-produced and slapped together by a robot. The influx of low-priced optics even secured my foothold a bit. However, after spending close to a week at the Leupold optics facility, the difference between the two became clear. Leupold designs, machines, assembles, and tests their products in Oregon. Additionally, with the exception of only a few lenses, every component is domestically sourced in its rawest state. This affords Leupold more control in terms of machining, coating, and overall optical engineering. This was explained in great detail by Shooting Sports Marketing Manager Nic Kytlica as he walked us through the factory floor.
Our tour began with what is realistically the end of the process: recycling. Consisting of a broad team of outdoorsy folk and conservationists, it was of little surprise to see that Leupold goes to great lengths to reduce its carbon footprint and mitigate waste. Every scrap of metal is compressed into ingots and returned to foundries for a second shot at becoming something you’d find on a store’s shelf. Ironically, just next door is where the process all begins, at the bar stock warehouse. No pre-formed tubes here; if it’s made of aluminum, it’s machined in-house. Naturally, this applies to maintubes but, surprisingly, even finer components like turret caps. As we passed bins and shelves of optics in varying stages of completion, some interesting manufacturing details were explained to us, many of which I cannot repeat. Among them was the process of CNC threading the turrets, which takes longer but yields more repeatable tracking and return to zero than conventional methods. The pinnacle of the tour was the trip through the optics lab. After covering our feet in plastic, we carefully strolled through the clean room and watched immensely skilled workers assemble and inspect optics in a way that can only be described as art. Watching somebody place a reticle under a microscope was awe-inspiring. It also implied the great deal of care and appreciation that Leupold has for its employees, as there is no training program on earth that can teach the instincts and talent they possess.
We approached the final stages of production with a peek into the finishing room. This is where we learned that Leupold utilizes an interesting process to impart that signature hue to their scope bodies. Often confused with Cerakote, the finish is actually traditional anodizing applied over a surface that is first bead blasted. This ensures that it can’t be rubbed off and doesn’t change any tolerances. From here, the products are laser engraved with any markings they require before undergoing a lengthy quality-control check that includes complete submersion in a dunk tank. If the piece has what it takes to represent Leupold’s best work, it is off to packaging and distribution. Once we knew where Leupold’s optics came from, we turned our attention to where they wind up.
Our first day on the range began with an introduction to Leupold’s Chief of Range Operations, Colby Ingram. Working alongside Brenton Baer, Matthew Hays, and John Snodgrass, the team would put us through an optics 101 course before helping us score impacts at distances in excess of 1,600 yards. But first was scope mounting. Prior to this portion, we were introduced to the company’s Mark 5HD 5-25X precision riflescope. Features like a 35mm maintube, enhanced glass coatings, and well-thought-out reticles make it perfect for long-range engagements if properly affixed to a quality rifle. Like many others, I found out that I was putting far too much work into this simple procedure. Ingram demonstrated a process that addresses one ring at a time for a fast, effort-free mounting job. After locking the second ring down, we confirmed that the dreaded reticle shifting didn’t take place and moved on to a ballistic presentation by Hornady’s Marketing Communications Manager, Seth Swerczek. The main topic here was the company’s 4DOF technology and how it provides fire solutions that are superior to traditional ballistic calculators. In short, 4DOF stands for 4 Degrees of Freedom and incorporates the bullet’s angle of attack into the equation. This is important because all solutions will include any vertical displacement created by a crosswind or tailwind. Furthermore, the entirety of the solution is based on the bullet’s drag coefficient, not its ballistic coefficient. This method compares your projectile to itself instead of a standard projectile. It does this by incorporating 437 data points that are unique to that specific bullet into the equation. Using Hornady factory 6.5 Creedmoor ammunition with a Seekins Havak HIT rifle, we were told first-round hits were the norm out to extreme distances; then, we were invited to test the claim.
In short order, we hit the range, zeroed our optics, and engaged steel out to nearly a mile. With more than half a dozen shooters on the line, dealing with an 8- to 10-mph wind, hearing hit after hit made this an engaging event. Even through the wind, the guns were capable of putting factory ammunition dead center using the data spit out by the app. Our scopes were built with the PR2- MIL reticle set in the first focal plane. This gave us unique quarter-mil wind holdovers in any power setting. I found this interesting as tenth and two-tenth holdovers are more common. However, by stretching things out, the scope becomes far less cluttered. Most targets are large enough that the finer scale isn’t missed, leaving us only with greater spotting ability. Our second day on the range began with a refresher, with extra emphasis on using the top-mounted DeltaPoint Pro red dot to quickly acquire a target. This was because we would be testing the equipment off an array of PRS-style shooting props. Learning how to use Armageddon Gear Game Changer bags for support, the team demonstrated some excellent marksmanship skills from less-than-perfect shooting positions. The lesson that I took away from this experience is that it pays to have a generous eye box, like that of the Mark 5HD. This ensures you’ll be able to use your scope in precarious positions. This became even more apparent when we moved to another area of the range and had to shoot at extreme angles. Hats off again to Hornady for its 4DOF software, as it compensated for this offset and allowed for first-round impacts on even my furthest target.
On the last day, we dragged ourselves out of bed before first light to get a true understanding of what makes a Leupold optic worth the extra coin. In groups of three, our hosts set up tripods containing a Leupold optic and then one from another manufacturer in the same class. I found scopes that looked good under fluorescent lighting could not resolve the shadowy areas of the range, whereas others were completely off with regard to color. Many target scopes disappointed us, as they only proved useful under full daylight. If you’re up first at an early match, that could spell disaster. I took a little extra time to play with parallax adjustments and found Leupold’s markings to be accurate, which wasn’t the case for many others. With the sun now well over the horizon, the demonstration was complete, and we moved on to another full day of shooting. After turning in our Havak HIT, we were issued a Seekins SP15 MSR chambered in the new Hornady 6 ARC. Intended for intermediate-distance targets, each was topped with a Leupold Mark 5HD 2-10X optic with the same quarter-mil wind holdovers. This flattened the learning curve and eliminated the chance of careless errors, making it an excellent companion to the 5-25X. Many of the same shooting positions were utilized, except we expanded into unknown distance targets. Using the mil marks through our scopes, success beyond our expectations was achieved, and I stepped off the range contemplating a 6 ARC as my next build.
My time at the Leupold facility showed me the value of buying an optic that is made by shooters. Moreover, purchasing their optics goes a little further toward securing American jobs. Throughout the experience, I gained appreciation of what goes into a wellbuilt optic and got to witness more than a dozen withstand rough service without a single failure. That just might be the best takeaway of the entire event; low-price optics work well, but Leupold optics always work.